Introduction
EVO machines are born to address specific or generalized industrial challenges, providing innovative solutions.
Problem Identification
A general example is the drilling of calibrated holes in hydraulic turbine disc joints, where limited space makes traditional drilling impractical. The R&D team analyzes the problem, considering work conditions, ergonomics, and operator habits.
Project Specifications
Project specifications are drafted, defining performance requirements, measurable and non-measurable properties. Emphasis is placed on crucial aspects like ergonomics, adaptability to operator habits, and intuitiveness of controls.
Solution Ideation
This phase is the most exciting: every team member, beyond their specialization, is free to propose one or more solutions. Each solution is analyzed and discussed to identify strengths and potential technological challenges.
Concept Phase
After selecting the potentially most advantageous solution, the team enters the initial concept phase. A simplified concept with basic mechanisms is developed, subject to further discussions and revisions.
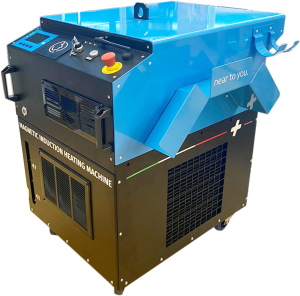
Sizing and Simulation
Through internal simulations (mechanical, electrical, thermal, and multi-physics), components are sized and simulated, guiding the project’s details, from defining each screw to costing components.
Prototyping and Testing
A prototype is built and tested. During installation, the operation is verified and recorded. Operators provide feedback, and if possible, the machine is instrumented to verify sizing calculations.
Testing and Optimization
Testing is repeated with different operators, pushing the machine to its maximum performance. Every part is carefully checked to ensure maximum efficiency.
This way, from concept inception to prototype realization, EVO machines tackle industrial challenges with innovation and precision. Our commitment to quality and efficiency is reflected in every stage of the process.